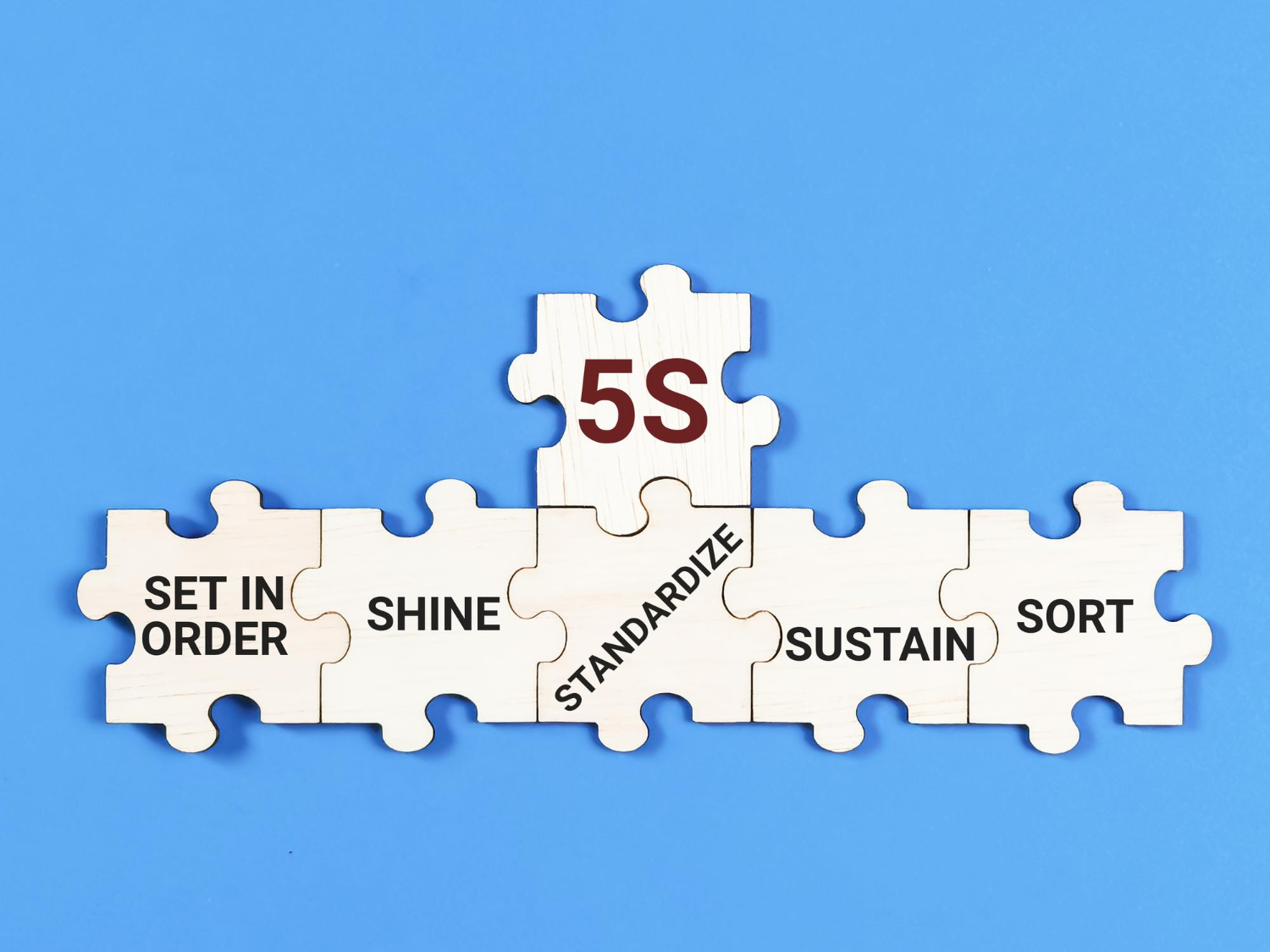
If you’ve ever taken part in the rollout of a serious 5S initiative, I’m guessing this question may have crossed your mind at some point, at least once.
Just for clarity, what I’m referring to here as “5S” is the visual management system that takes its name from 5 words in the Japanese language (Seiri, Seiton, Seiso, Seiketsu, Shitsuke) and has been deployed in organizations of all shapes and sizes around the world, in varying degrees, for several decades.
In my personal experience as a Honsha associate, and having had the opportunity to guide and coach 5S implementations for over 20 years, the reason why 5S is so difficult to implement correctly, I believe, can be stated as follows… Because 5S relies heavily on the successful integration of People, Purpose, Process, and Problem-Solving. If the need for this integration is not clear to those deciding to formally establish a 5S system, then the correct implementation of 5S can truly become very difficult.
Let’s break down these four ‘P’ of 5S, to see how they work together.
P1: PEOPLE
We know that ‘resistance to change’ is as normal as the search for happiness among humans. Neuroscience shows us that our brains are designed to “repeat the known” as an automatic mechanism for preserving energy, by avoiding decision-making processing whenever possible, as much as possible.
Preferring to do things “as we’ve always done them” is arguably the result of our brain preserving energy for critical processing tasks (typically related to the unfamiliar or unknown).
By acknowledging and accepting this natural human response, we can find better ways to overcome it, rather than trying to fight against it when introducing new 5S practices and routines into a workplace.
Some people are ‘messy’ by nature, and may even feel more creative, free, or even cozy in an unorganized environment. In the bell curve of ‘human orderliness’, we will naturally have some portion of people that match this ‘messy’ description and it’s also likely that we would find them in all kinds of organizations. Although this may mean potentially facing a higher challenge when implementing 5S (sometimes even conflict), if we recognize ‘messy’ as a normal character trait, while also honoring the principle of ‘respect for people’, this can help us gradually bring everyone successfully along a 5S journey with empathy and patience.
– Hopefully, the ‘messy’ people in your organization are not in key leadership roles. Otherwise… good luck!
Although I say ‘good luck’ with intended humor, you may agree that in most any hierarchical organization we can find evidence of the saying “what’s important to my boss is important to me”; therefore leading by example and modeling the behaviors we wish to see in our people go a very long way when leaders not only promote 5S activities, but personally participate and contribute actively during the rollout and the periodic upkeeping of 5S.
As in most any human undertaking, a perception of benefit (the “what’s in it for me”) must be very clear at every level of an organization, for people to willingly accept change. If our 5S initiative is not felt as personally beneficial to our team members on the front line, going all the way up to our senior leaders, then 5S will not take hold …and will definitely not last.
A perception of benefit, in the case of 5S, means that people at all levels can clearly recognize that the system is helping them reach their goals in a more error-free, simpler, and less-strenuous way.
For the above perception to become a reality, organizations that are committed to 5S also focus highly on the next ‘P’.
P2: PURPOSE
Initiating a 5S implementation without understanding (and clearly communicating) the purpose of 5S can produce many undesirable outcomes. I would personally discourage anyone from starting a 5S initiative if they are not fully certain of the true purpose of 5S.
Although many things can be said about the huge benefits and great outcomes of 5S, its purpose (as recognized within the Toyota Production System [TPS]), can be summarized as follows: “The purpose of 5S is to make waste evident”.
By “waste” we are referring to The 7 Wastes, as formulated by Taiichi Ohno*. These wastes are: motion, transport, correction, waiting, overprocessing, inventory, and overproduction.
But why make evident the existence or emergence of these wastes in an organization? To quickly bring the work environment and its elements back to their defined ‘ideal condition’ (or standard), before the identified deviations escalate to larger problems.
The above implies that we would need to predefine and make clear what those ‘ideal conditions’ (standards) must be and look like, in order to have a reference against which to compare any current situation. This brings us to our next ‘P’.
P3: PROCESS
Implementing 5S correctly means having in place the following Process elements…
- Visual Management that provides “status at a glance” to most anyone within a workspace or area. This means having the necessary visual information and detail for people to understand and confirm what exactly it is that they are looking at (tools, supplies, equipment, locations, etc.), where is it that these elements should be located, as well as how many (or how much) should be available at any given time, to avoid waste. If the 5S’d area in question provides clear information on descriptions, locations and quantities at a glance, we can feel confident that we have the proper level of visual management for 5S.
- Standardized Work (SW); displayed in the form of documented, people-focused tasks or routines to be followed step-by-step on a periodic basis; ensuring that an area that has undergone a 5S transformation will remain as defined, over time.
The SW for 5S is typically found in the form of auditable documents, that are visible in the workplace, and describe the ‘what’, ‘who’, and ‘when’ related to the tasks that must be regularly performed to consistently maintain an area within its defined 5S standards, along with providing a pictorial or photographic reference of how the 5S’d area should look (contributing to visual management). - Leader Standard Work (LSW). In the case of 5S, LSW refers to the predefined, routine and periodic activities that Supervisors, Middle Managers, and Senior Leaders are committed to perform in support of the organization’s adherence to 5S principles.
At the Supervisor level, this would mean regularly checking/inspecting the status of the areas that have undergone a 5S transformation, against their Standardized Work documents and 5S Visual Management elements, while providing immediate feedback and guidance to those responsible for performing the Standardized Work portion of 5S, in case of deviations.At the Middle Manager level, the support commonly is in the form of monthly 5S audits, which are scored and reported against clear criteria previously taught and coached to all members of an organization, as part of the training portion of a 5S implementation.
For Senior Leadership, the LSW of 5S is commonly related to the issuing of quarterly reports that internally communicate 5S trends (based on the monthly 5S audit results) while providing people or areas with encouragement and/or praise, as well as support and resources, if and when necessary for the proper health and long-term sustainment of the organization’s 5S system. Note: In some organizations, Senior Leaders also participate in portions of the monthly 5S audit process; demonstrating to all the importance they place on 5S, and seizing the opportunity to witness first-hand where additional support or perhaps their personal guidance may be required.
Summarizing the process elements described above, we find that within an organization committed to 5S there are specific 5S standards to be followed, along with formalized methods to periodically confirm ‘plan versus actual’. This means that problem-awareness (the acknowledgement of 5S deviations) can make its way from bottom-up in an organization; while support, resources and guidance can be provided from top-down. In other words, there is the baseline structure necessary for our next ‘P’.
P4: PROBLEM SOLVING
Problem-solving can take many shapes and forms, from reactive troubleshooting to creative innovation**.
In the case of our topic, we are talking about regularly solving problems to help the organization’s 5S system continually meet its purpose of “making waste evident”, as well as to support the continuous reduction (if not elimination) of the ‘7 Wastes’.
Here’s a real-life example. Since my initial years as a Lean consultant, I have conveyed the following information and instruction as part of a typical day-long 5S training workshop:
“Items in a 5S’d area (meaning tools, materials, supplies, etc.) should be…
- Easy to See
- Easy to Take
- Easy to Place Back”
These 3 points make total sense, right? Simple and logical. Nothing to object to.
Interestingly, though, the true value and deep meaning of these points (especially the third) became evident to me only after some 5 years of coaching and guiding teams in 5S implementations; with dozens of training sessions and a few hundred trainees to my name. – A humbling experience, no doubt.
The ‘revelation’ for me at the time meant understanding that… “if the 5S standards we define for a workspace are not truly easy for people to follow as they perform their work, then we are potentially creating problems for people, while expecting them to adhere to a 5S system that is in fact adding waste (of motion, transport, etc.) to their workday.”
To avoid this situation, a key problem-solving task within 5S (for coaches, guides, or leaders) is to ensure that any 5S standard, rule, or guideline incorporated into a workplace is actually very easy to follow (along with waste-revealing); otherwise, people will eventually tend to stop adhering to the 5S standard, in order to quickly ‘get back’ to their value-adding activities; despite their best intentions and also regardless of how well-designed and nicely organized a 5S’d area may seem.
Many times, repeatedly failing to follow 5S standards (such as not putting things back in their proper place) can also be due to a ‘short-term mentality’ when considering the importance and priority of 5S.
I would agree that if someone is facing a critical problem at work, such as the breakdown of a bottleneck-process or the delay of an urgent shipment, then the task of ‘placing a tool back in its exact spot’ (for example) can at that moment be perceived as something trivial or irrelevant …from a short-term perspective.
However, if Supervisors and leaders in general, fail to react ‘on the spot’ to 5S deviations (by not raising awareness, understanding the cause, requesting correction and coaching their people on the importance of adhering to standards), then one small 5S deviation can gradually (but surely) turn into multiple 5S
deviations, of increasing size and complexity; until the task of bringing an area back to its ‘ideal’ (or standard) 5S condition would require such time and effort, that it could not be done without significantly disrupting the organization’s value-adding work activities. – At that point, we’d have a considerable 5S problem.
Applying problem-solving within 5S, seen from a purposeful long-term perspective, then means that supervisors and leaders are always reacting ‘on the spot’ to observed deviations; understanding that these deviations, however small, will eventually impact the organization’s ability to consistently add-value over time, if ignored or overseen.
In conclusion (and coming back to our initial question), a true commitment to 5S requires integrating People, Purpose, Process, and Problem-Solving; which can be done with less effort when we acknowledge human tendencies, understand and clarify our purpose with 5S, and support our formally defined processes with continuous problem-solving; all of which remove the common difficulties associated with implementing 5S correctly …and they also ensure that the benefits of 5S will endure in our organizations, for as long as we remain consistent.
Best wishes for success in your 5S initiatives,
Paco Estrada.
.
.
Francisco (Paco) Estrada.
With over 20 years of experience supporting the implementation of TPS/Lean methodologies in very diverse industries and as a senior associate of Honsha.ORG, alongside Toyota senseis, Paco has contributed to the Lean transformation of numerable organizations, in 11 countries.
..
..
*Taiichi Ohno is considered the Father of the Toyota Production System. Here you’ll find a short Bio from ‘The Economist’: http://www.economist.com/node/13941150
**Smalley, Art (2018). Four types of problems. Lean Enterprise Institute.
Your Content Goes Here
Your Content Goes Here