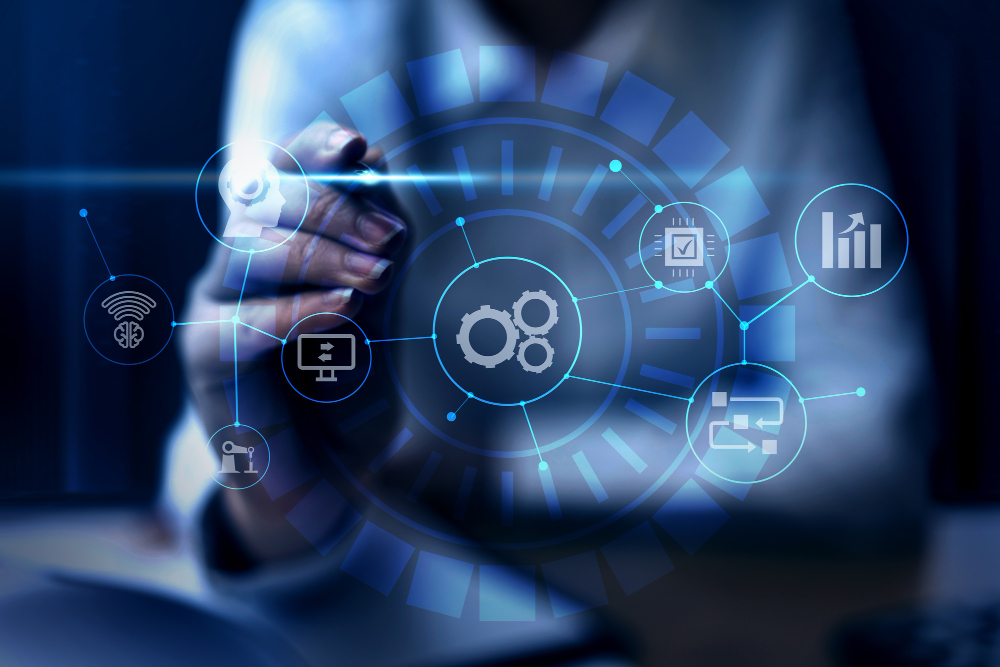
Everyone knows that Lean thinkers and IT (Information Technology Department) have an open war going on. Lean advocates complain that IT is slow to come to the Lean table (so to speak) and traditional IT solutions are the biggest stumbling blocks on the way to implementing the Lean Supply Chain. The contempt of the leanest of Lean thinkers for IT is demonstrated by the “NO MRP” buttons.
Of course, the role of MRP is changing, but as a forecasting tool, MRP is the key to capacity planning, sales planning, and procurement with long lead times or goods on allocation. Material release based on the end consumer’s pull signal replaces the logistics component of MRP. The next generation of Lean Enterprises will use IT and the Lean Supply Chain as a strategic advantage. These rare organizations will not only integrate IT into the Lean Supply Chain, but will leverage IT to reach new levels of Lean in eliminating waste in operations and logistics structures.
We all know that Processes come before Systems. But do we know what the Lean Distribution processes will be? Can we say what kind of System will be needed to support these processes? Let’s explore some of these possibilities:
Communications: As pull signals replace the traditional MRP release of materials and the company takes advantage of the demand-driven supply network; instant end-to-end recognition will be essential for short replenishment lead times. Someone could use cards in a closed-loop transportation system with multiple daily deliveries, but cards wouldn’t travel well. IT will need to collect the demand, organize it according to the replenishment route and send it all through the Lean Supply Chain.
Of course, this is old news; it’s basic, but what you do with the data is what makes it a Lean Supply Chain.
Transaction Costs / Structure: The biggest barrier to using more frequent demands is the transaction cost of developing and processing Purchase Requisitions (PRs), including checking the material against the PRs on receipt. The key driver for large quantities of purchases in the formula for Economic Quantity in the Requisition is the cost of the Requisitions. A special place is reserved for those poor souls in receiving with the difficult task of trying to identify what happens on arrival versus the record in the system. No wonder Purchasing is reluctant to create yet another CR. The Lean Guru is asking for CRs for 1 unit. I shudder to think what would happen in Accounting.
IT will be driving Requisition costs down to near zero. Traditional CR’s will go, replaced with CR as events including Kanban Cards, either daily or posted several times a day. The CR will no longer be a discrete event, but will embody a relationship and set the conditions for accepting postings. Price assignments will be a set of data shared between supplier and customer, invoices will be created on receipt of the Kanban and payment will be generated by Receiving on the basis of pre-established time, without an invoice. It will seem so easy, most of us will wonder why it took so long.
Kanban and Maintenance Planning: Even Lean advocates are begging for a solution to Kanban Cards and Maintenance. Anyone who has calculated Kanban circuit sizes and printed and unfolded cards knows that this is no easy task. And those who have had the misfortune of running out of a Kanban item can attest to the feeling that you really don’t know why. Creating a Kanban system for a distribution center with tens of thousands of items makes an assembly plant with a few thousand look like a piece of cake.
IT solutions will not only determine the number of kanbans, but will also monitor operations and determine when the number of kanbans should be adjusted. Reducing the amount of materials when appropriate will be where IT can be harnessed to reach new levels in Lean. The systems will also transmit kanbans in an appropriate format to those not in the loop and put an end to the work of checking and routing at the docks. For all those who are looking for the standard format for Kanban, before long it won’t exist or won’t need to exist.
Operations Planning and Control: Mr. F. Cho when he was the President of Toyota Motor Corporation once said that Lean in the assembly plant was easy compared to a Distribution Center. The plant has a chained conveyor belt that presents a job every 60 seconds; the operator is prevented from advancing or delaying the job. In the Distribution Center there is no set rhythm. Just ask them if they are early or late. To a man, they’ll say they’re late or will be late if they don’t collect as quickly as possible. Even in automated warehouses, there is no rhythm. It seems that automation supports larger and larger picking batches by optimizing picking, while getting worse at sorting and packing. (For all the Taylorians who believe that reducing waves is the way to be more efficient; we ask: why not one wave a day or one a week? Why not one wave per month?).
IT will support the Lean Supply Chain by dramatically improving Distribution Center operations through more frequent ordering and replenishment. What we expect is that systems solutions will analyze the level of work for the day, establishing a number of pickups and receipts of requisitioned batches to maintain performance objectives, establishing TAKT time according to the normal work window, determining operator numbers according to the cycle times of standard work batches and notifying supervisors if overtime is required. When operators are available, supervisors will be given a selection of inventory, cleaning or other batch types for the system to dispatch. Operators will be reserved for problem-solving projects according to the Distribution Center’s objectives. Every time the system creates a plan, it will automatically level out waves of picking versus sorting and packing based on the content of the job.
Expecting this doesn’t stop the development of the plan. The system will also continuously monitor progress and record problems for future troubleshooting and inform supervision when an inventory is needed. Operators will be transferred from one activity to another without interruption, with the system controlling the time according to the calculated TAKT and task group assignment. If additional work is received, the system will analyze the work and make the appropriate calculation to develop a new plan, which will be executed without intervention. The revised task groups will simply flow to the operators or if necessary to labor allocation.
In the new IT solution, when the DC (Distribution Center) Manager is asked: “How’s it going?” He will reply: “Great, the plan is to ship 100 boxes in the first hour and we’ve already shipped 99. Wait! The 100th has just left. For now we usually have 14 batches that haven’t been completed according to plan, usually 10 take less time and 4 take more. Today we only have 9 – 7 early, and 2 late. The Kaizen Team is really making some progress. We’ve just received the rest of the replenishment for the order that was placed 10 days ago, only 2 days more than the transit time.”
As you can see, IT will be an integral part providing: media to communicate demand, developing processes that reduce structure and operational improvements. Traditionally we look at past productivity performance as a way of judging how we’re doing. We don’t really know how to change the number that has been reported. Unallocated time and lost time due to problems that have been encountered are the biggest obstacles to improving productivity.
We think organizations will need to move away from traditional problem solving as they move to the environment where the pace is set to meet customer requirements instantly. The system will collect key data and present it in a way that operators will instantly have a proper understanding of the current condition. Everyone’s problem-solving ability will be enhanced by the availability of data that is supported by the systems that will be developed.
We are excited about the future and look forward to your comments. Please email questions or comments to Dan Mulloy: d.mulloy@honsha.org.
Dan Mulloy
Dan’s career has spanned more than 30 years with General Motors and Toyota Motors, learning and applying the principles of the Toyota Production System in a variety of manufacturing, engineering, logistics and distribution environments. His in-depth knowledge of vehicle manufacturers’ supply chain, manufacturing strategy and purchasing activities provides a uniquely detailed perspective on the key attributes and differences of each.
He gained practical experience of the lean supply chain when he worked directly with Toyota experts as Project Manager, transforming Toyota NA’s service parts supply chain through TPS/Lean. The project included the re-engineering of the spare parts layout and the complete transformation of the daily receiving/collecting operations. This project was cited in “Thinking Lean” by Jim Womack and Dan Jones.
Dan was immersed in Toyota’s methodology as part of the Strategic Planning team and gained practical knowledge of Toyota Kaizen by training facilitators who drove improvement projects throughout the parts distribution centers. In this role, he was responsible for developing the overall Kaizen strategy, including evaluation criteria and an annual celebration. At Toyota, he conducted Hoshin Kanri workshops and A3 training.
Click here to read other articles from Honsha.ORG.
Follow us on YouTube.
Your Content Goes Here
Your Content Goes Here