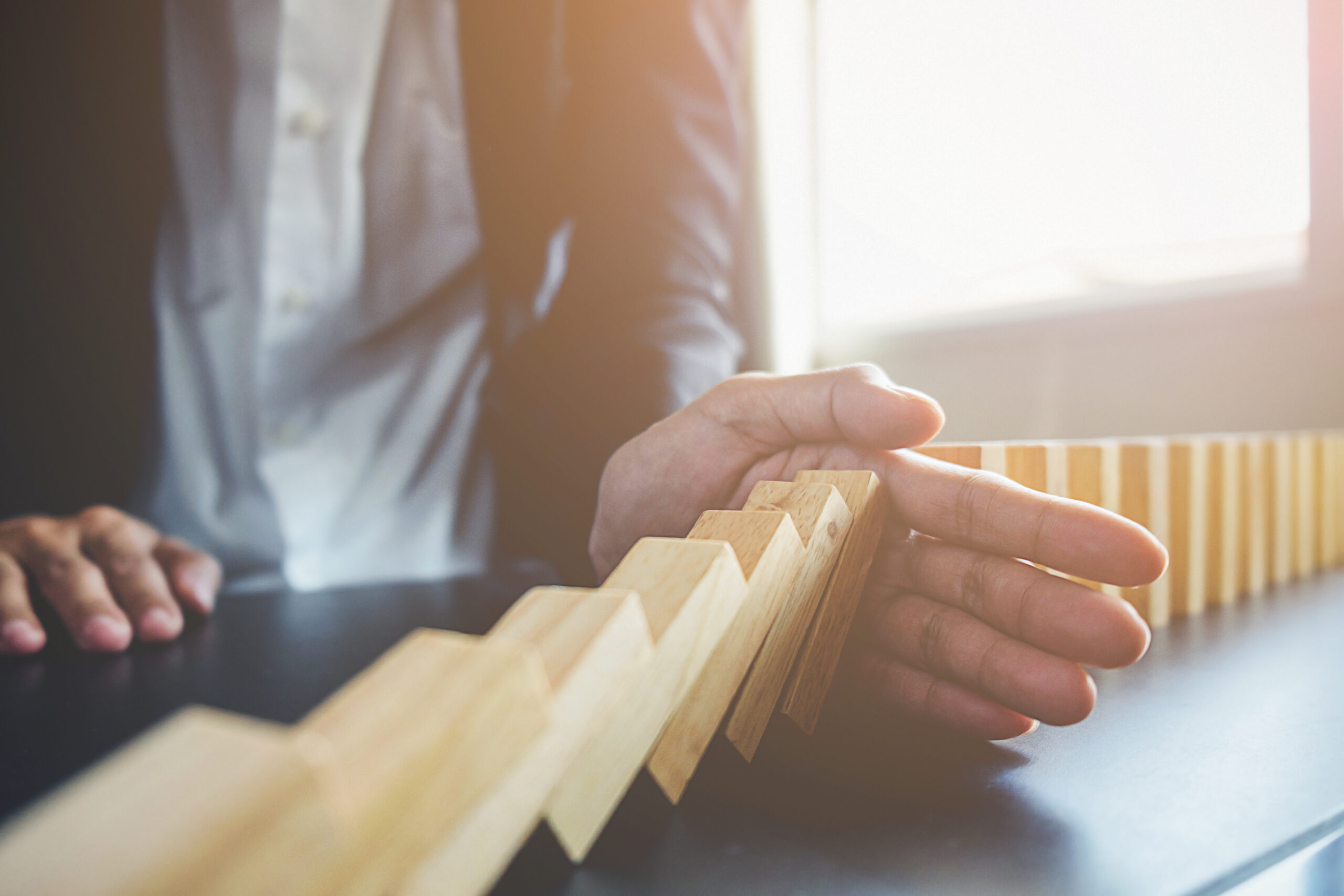
I confess to having used solutions like these several times at the start of my career when I was still unaware of Lean techniques and believed that it was impossible to avoid human error; and in a way I tolerated a small proportion of error. To answer this question, let’s look at a case that happened a few months ago in a hospital in São Paulo: a 12-year-old girl with the symptoms of a simple viral infection lost her life due to a mistake, an oversight on the part of a nurse who mistakenly applied petroleum jelly instead of the prescribed medication; the mistake could not be repaired and within a few hours the girl lost her life. So a common human error defined the tragic fate of this little girl; I ask again, is human error tolerable?
In this case, a simple mistake is unacceptable and it’s natural to think that it was carelessness on the part of the nurse not to check the medicine before administering it; but, on the other hand, we should consider the following: how many times have we gone to the market and ended up buying a product by mistake because of its external appearance? It’s such a common mistake that some less ethical companies use images similar to famous products on their packaging to take advantage of this human error.
So before we continue, I think it’s interesting to add a classification of human error: according to studies carried out by James Reason (1990 Cambridge Univ. Press), there are two types of error, the first refers to intentional execution, where the author of the action had the intention of carrying it out in the way it was done, either through sabotage or lack of knowledge of the correct way, and where solutions such as training, work instructions and disciplinary measures apply with some effectiveness. In the second type, unintentional errors, which are the result of distraction or forgetfulness, the previous solutions do little or nothing to solve the problem.
In any case, the nurse, who quickly became the “villain” in our case, has had her career destroyed, will be prosecuted for murder, could be imprisoned, and on top of all this we can believe that this mistake has marked her life forever and she will carry the weight of this mistake on her conscience. So I ask you: did she make this mistake with intent, either through lack of knowledge or sabotage?
This is definitely not an intentional mistake, the nurse had no intention of murdering the patient, nor did she apply the Vaseline knowingly, but without knowing the consequences of such an infusion. The fact is that she applied the substance assuming that it was the prescribed serum, so it is clear that this is an error due to distraction or forgetfulness.
So I don’t believe that in this case the nurse is to blame, but rather the victim in the story; I base my analysis on the details and information available in the media about this problem. The bottle containing the two substances was identical, differing only in the information on the same-colored label, and the Vaseline bottle was located in the same cupboard as the serum bottles; all of this, coupled with a stressful, high-volume environment in a popular hospital with a heavy workload on its employees, creates a perfect breeding ground for errors and mistakes of this kind.
Training, firing, implementing new instructions in the workplace will not prevent another nurse from making the same mistake, because with the facts described the impression is that it would be much easier to make a mistake than to do the right thing, wouldn’t it? I’m sure I’d make the same mistake as the poor nurse, and the challenge is, who wouldn’t?
But if we shouldn’t tolerate human error, on the other hand we should understand that making mistakes is inherent to being human, how should we proceed?
In my opinion, we have a tendency to justify mistakes instead of addressing them and trying to resolve them. It’s simpler and quicker to find a culprit and be content with that, even if the solution to the problem lies in a simple analysis that could prevent the error altogether.
That’s why I invite you to do a lean analysis, starting with the five whys technique in this case:
Why did the girl die?
Because the nurse mistakenly applied Vaseline to her blood instead of saline.
Why did the nurse apply the Vaseline by mistake?
The nurse didn’t read the product’s identification label
Why didn’t the nurse read the label?
The nurse took the Vaseline and the serum from the same cupboard and assumed they were the same substance.
Why were the Vaseline and the serum in the same cupboard?
The packaging was exactly the same for both products and didn’t allow for a physical barrier to prevent improper storage
Our analysis shows that the fact that the packaging was the same for two completely different products led to two errors: firstly, the location of the Vaseline in the wrong cupboard and, consequently, the improper application of the Vaseline to the patient.
As both products were packaged internally, we can suggest that packaging is a factor under the hospital’s control and easy to change, so packaging is the root cause of this problem.
As proposed by the hospital itself, the use of different colors for the label would allow immediate visualization of the contents, in addition the packaging could be altered with the addition of references or physical barriers that identify the product and its storage location, preventing these products from being improperly stored, i.e. this consists of the application of another lean technique called Poka Yoke (Japanese word meaning error proofing).
The Poka Yoke technique consists of designing simple devices to identify and alert when something is not being done correctly, requiring immediate correction, and is the most effective way of avoiding human error.
Within the lean culture, Poka Yoke also acts as fuel for the process of continuous improvement, being simple and inexpensive devices; companies that apply lean motivate their employees to develop these devices for all their day-to-day activities, preventing errors.
Using the Poka Yoke technique, we could go further and develop Poka Yokes for the connections with specific formats for each type or family of medication, allowing a doctor to define which medications and medical equipment have connections compatible only with the prescribed medication, eliminating the risk of using the wrong medication, among other human errors related to a hospital’s routine.
In short, making mistakes is inherent to human beings, but that doesn’t mean we have to tolerate and live with them. Through Lean techniques such as Poka Yoke and Visual Management, it is possible to identify and correct human errors at source before they affect the process, generating an environment with 100% quality, using existing resources in the process and the intelligence of all the company’s employees, without massive investments in sophisticated and complex quality inspection equipment.
Renato is a mechanical engineer with a master’s degree in Manufacturing and Logistics Management (Unicamp). His specialization in Lean came from Toyota in Brazil, where he trained suppliers to comply with TPS requirements. He led the Lean implementation at Delphi Thermal and Interior in South America and was recognized by Autodata magazine as an important implementer, leading the Jaguariúna plant to be the most productive and profitable company per square meter among Delphi Thermal companies. Currently based in Indianapolis IN, USA, Renato leads the implementation of Lean at CTB/McGraw Hill. He has also been extensively involved in the exchange of Lean knowledge with organizations in Chile, Hungary, France, Poland and Portugal.
Click here to read other articles from Honsha.ORG.
Follow us on YouTube.
Your Content Goes Here
Your Content Goes Here