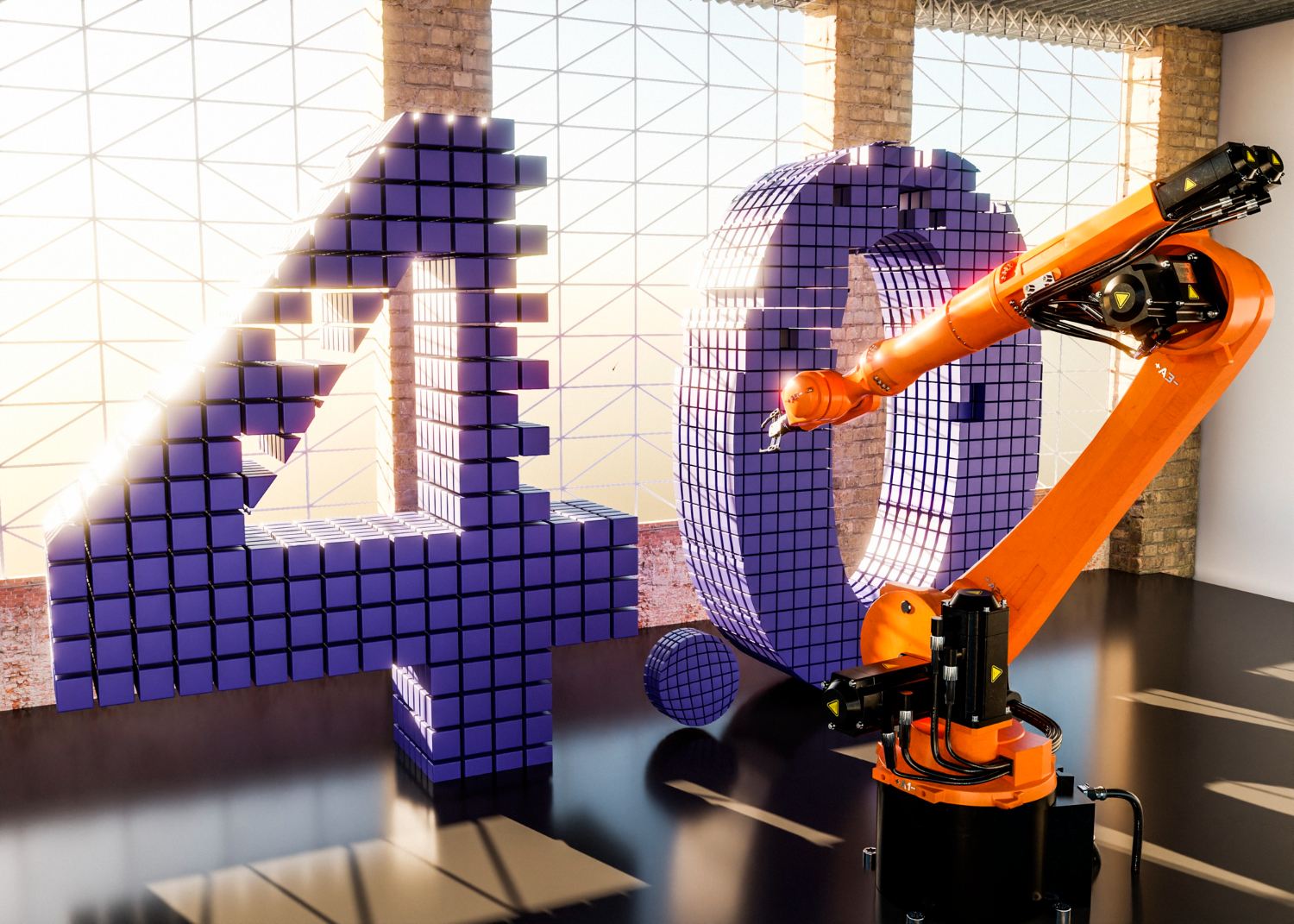
Why one and not the other? Or both? Are they incompatible? Are they complementary? Are they mutually exclusive?
Let’s go.
Lean has been around for a long time. Officially since 1937 with Just-In-Time. It became known in the United States in the 1970s, during the oil crisis.
I got to know Lean and started practicing it in 1994 in a Western company. This is when the book “The Machine that Changed the World” (1992), which many of you will have read, was released. At the time, I read it and was incredulous. I was amazed to be part of the transformation, getting my hands dirty on the factory floor, all together. It really worked!!!
In Brazil, very few companies had started down the Lean path with the support of SENSEIs. It was a tremendous culture shock and at the same time a privilege to have had that experience. Lean already had 57 years of history.
Since then, companies have made many efforts to follow the Lean path. The company where I worked did too. The first results were significant. A 50% increase in efficiency was achieved to everyone’s amazement. Then what must have happened at Toyota happened too. The gains were reduced, by 30%, 10%, 5% and then the companies began to question whether it was worth continuing down this path.
Today, then, at the age of 82, for many Lean has had its day, and is now a thing of the past. The future of manufacturing belongs to machines and modern information technology resources, such as the internet of things and artificial intelligence.
Industry 4.0 is coming with everything, heralding a technological revolution in the way we manufacture, changing traditional jobs, from the shop floor to factory management. Anyone who isn’t up to date will be ostracized.
But I am also a privileged witness to what Toyota has done over the years. It has continued with its management system, evolving consistently. The investments made have been in KAIZENs raised and suggested by its employees.
How are you preparing for the future? By encouraging employees to continue doing KAIZEN and by proposing ways forward. In the words of Executive Vice President Mr. Mitsuru Kawai of Toyota Motor Corporation: “If you teach a robot a task, it is able to repeat that task 10 times, 20 times, tirelessly. But to make that robot work better, you need someone who knows how to work better, who knows how to do KAIZEN and implement improvements in the details. A robot alone can’t do this. It always depends on a human being who is always striving to improve”.
Toyota doesn’t talk about Industry 4.0. It talks about KAIZEN. Invest where you see fit. Especially in its people, who are trained to eliminate waste wherever they are.
Toyota Annual Report 2018:
Evolution of the automakers:
(https://www.youtube.com/watch?v=OT5kjcrb9MY)
(https://www.youtube.com/watch?v=vudqr4gxRoM)
Dário Yanagita (d.yanagita@honsha.org)
Dário possui 30 anos de experiência em indústria automobilística no Brasil, dos quais 15 anos trabalhando na Toyota do Brasil. Possui especialidade variada, de usinagem, montagem, logística, qualidade e meio ambiente. Implementou linhas de produção Lean, programas Kaizen, geriu planos de desenvolvimento de equipes e transformação Lean em empresas.
Click here to read other articles from Honsha.ORG.
Follow us on YouTube.
Your Content Goes Here
Your Content Goes Here