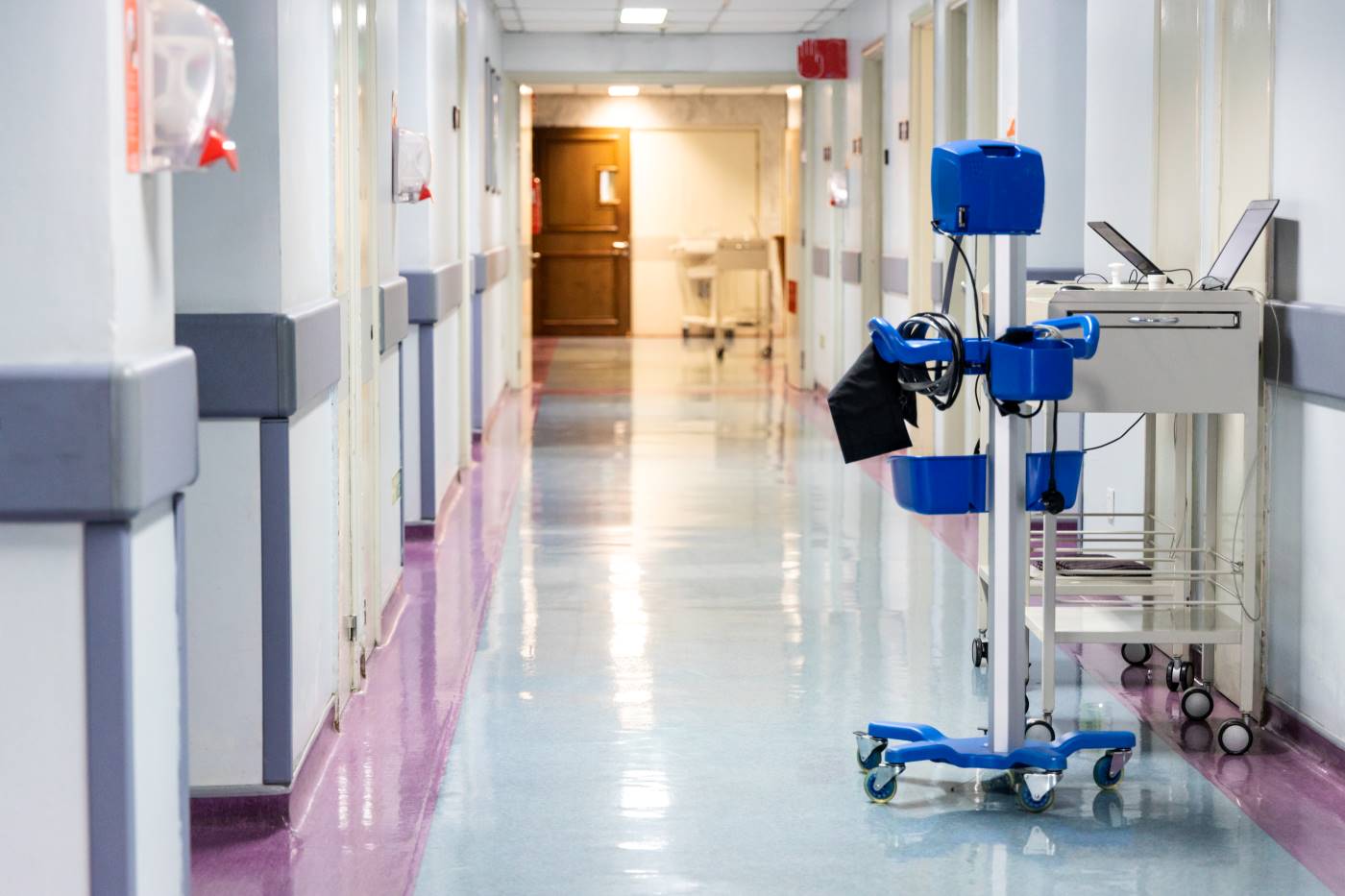
Lean and the Toyota Production System (TPS) are management methodologies developed by Toyota to improve efficiency and quality in automobile manufacturing. However, these methodologies can be applied across various sectors, including the healthcare segment.
The healthcare sector faces unique challenges compared to other industries, such as the need to ensure patient safety and service quality. Implementing Lean and TPS can help hospitals and clinics enhance their processes and services, leading to increased efficiency, quality, and patient satisfaction.
In this context, we will focus exclusively on the benefits that Lean and TPS can bring to the healthcare segment. We will explore specific examples of how these methodologies can be applied to improve process efficiency, elevate service quality, and enhance patient relationships. If you are a healthcare professional looking for ways to improve the efficiency and quality of your processes and services, read on to discover how Lean and TPS can help you achieve your goals.
Waste Reduction: Lean and TPS can help hospitals minimize waste in terms of time, materials, and resources. For example, implementing Kanban systems can help manage medication and medical supply inventory, preventing overstocking and loss due to obsolescence. Additionally, reducing setup times (equipment preparation) can decrease equipment idle time and enhance the efficiency of medical procedures.
Process Efficiency Improvement: Applying Lean and TPS can help hospitals improve the efficiency of their processes, reducing patient wait times and increasing service capacity. For instance, implementing standardized workflows can help decrease patient hospitalization times and increase bed occupancy rates.
Service Quality Enhancement: TPS is renowned for its emphasis on product quality. Similarly, applying Lean and TPS in hospitals can help improve service quality by reducing the occurrence of medical errors and enhancing patient satisfaction. For example, implementing quality monitoring systems can help identify areas for improvement and ensure compliance with safety and quality standards.
Increased Flexibility in Patient Care: Hospitals need to adapt quickly to changes in patient demand and market conditions. With Lean and TPS implementation, hospitals can become more flexible and responsive in addressing diverse patient needs, reducing response times and boosting patient satisfaction.
Enhanced Patient Relationships: Lean and TPS implementation can help strengthen hospitals’ relationships with patients by increasing transparency and communication. For instance, establishing feedback systems can help identify improvement areas and increase patient satisfaction with the care received.