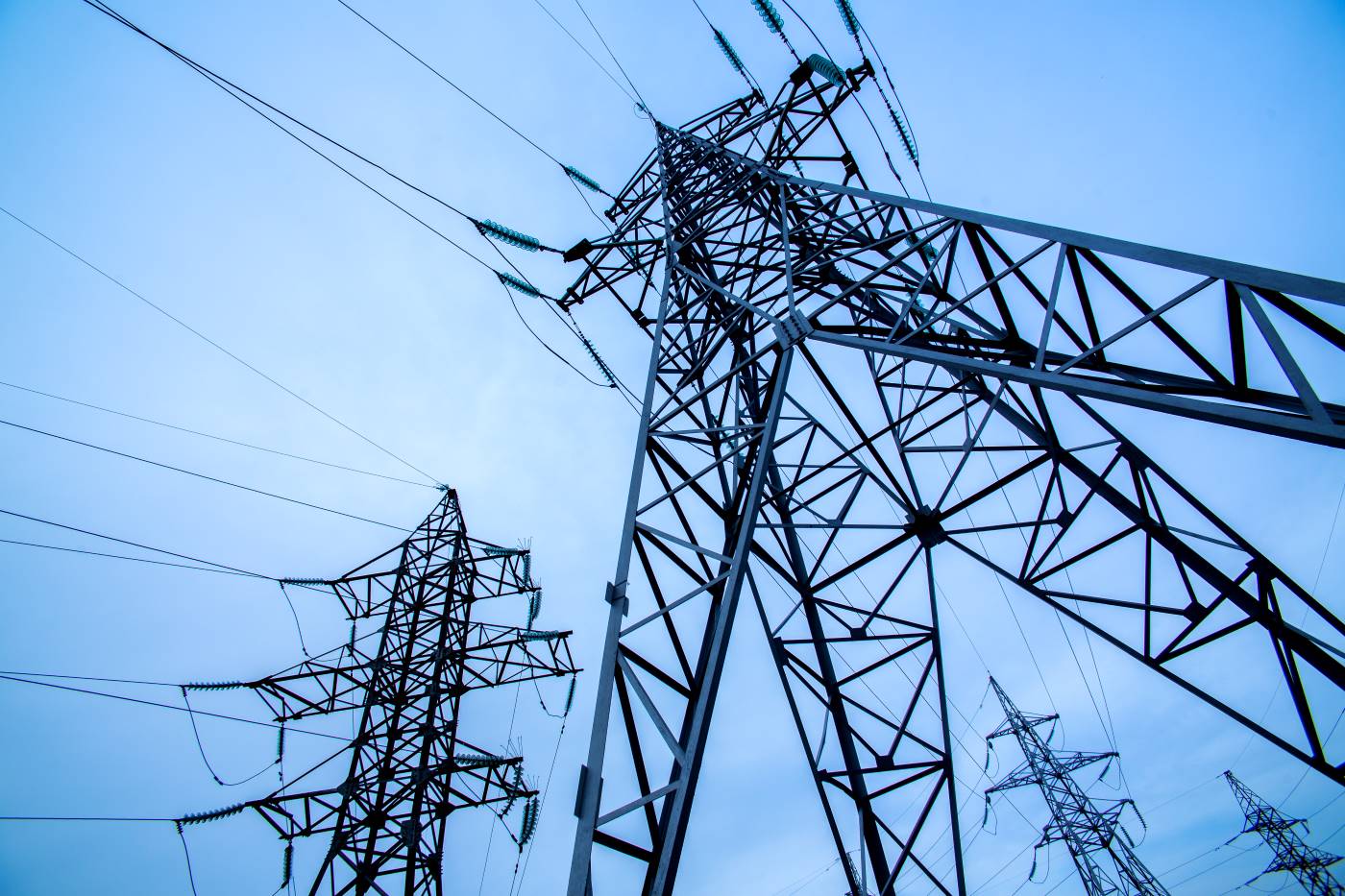
The application of Lean methodologies and the Toyota Production System (TPS) can bring unique benefits to the energy sector, helping to optimize production processes, reduce costs, and improve the quality of the energy produced. The energy sector is one of the most important and strategic sectors of the global economy, responsible for providing electricity, fuels, and other essential products to various segments of society.
However, the production and distribution of energy involve complex processes that require special care and can incur high costs. This document will explore, in an educational manner and with examples, the exclusive benefits that the energy sector can achieve through the implementation of these methodologies.
Reduction of Unplanned Downtime: The energy sector deals with electricity production, and it is often necessary to conduct corrective maintenance on equipment and tools to prevent unplanned outages. The application of TPS can help reduce unplanned downtime by implementing standardized workflows and utilizing data analysis tools to identify bottlenecks and areas for improvement. For example, a power plant can use Single-Minute Exchange of Die (SMED) to minimize equipment changeover time, thus increasing production efficiency.
Waste Reduction: The energy sector handles expensive and hazardous materials, such as fuels and chemicals. The application of Lean can help minimize waste by ensuring that materials are stored and utilized properly. For instance, a power plant can employ Lean principles to identify and eliminate unnecessary processes, thereby reducing production time and preventing the overproduction of energy.
Improvement in Energy Quality: The quality of the produced energy is fundamental to customer satisfaction and production efficiency. The application of TPS can enhance energy quality by reducing waiting times and increasing process efficiency. For example, a power plant can implement TPS to ensure that energy is produced accurately and with high quality, thereby improving customer satisfaction.
Enhanced Inventory Management: Inventory management is crucial in the energy sector, as many materials have expiration dates and must be stored appropriately. The application of Lean and TPS can improve inventory management by reducing excess stock and ensuring that materials are always available for production. For instance, a power plant can use Kanban to control fuel inventory and ensure that energy is produced quickly and efficiently.
Cost Reduction: The application of Lean and TPS can help reduce the costs of a power plant by eliminating waste and optimizing processes. For example, a power plant can use Lean methodologies to decrease energy production time, thereby increasing employee productivity and reducing operational costs.
It is important to emphasize that each power plant has its unique characteristics and can benefit in distinct ways from the application of these methodologies. Therefore, it is essential that implementation be carried out by specialized professionals with expertise in the sector.