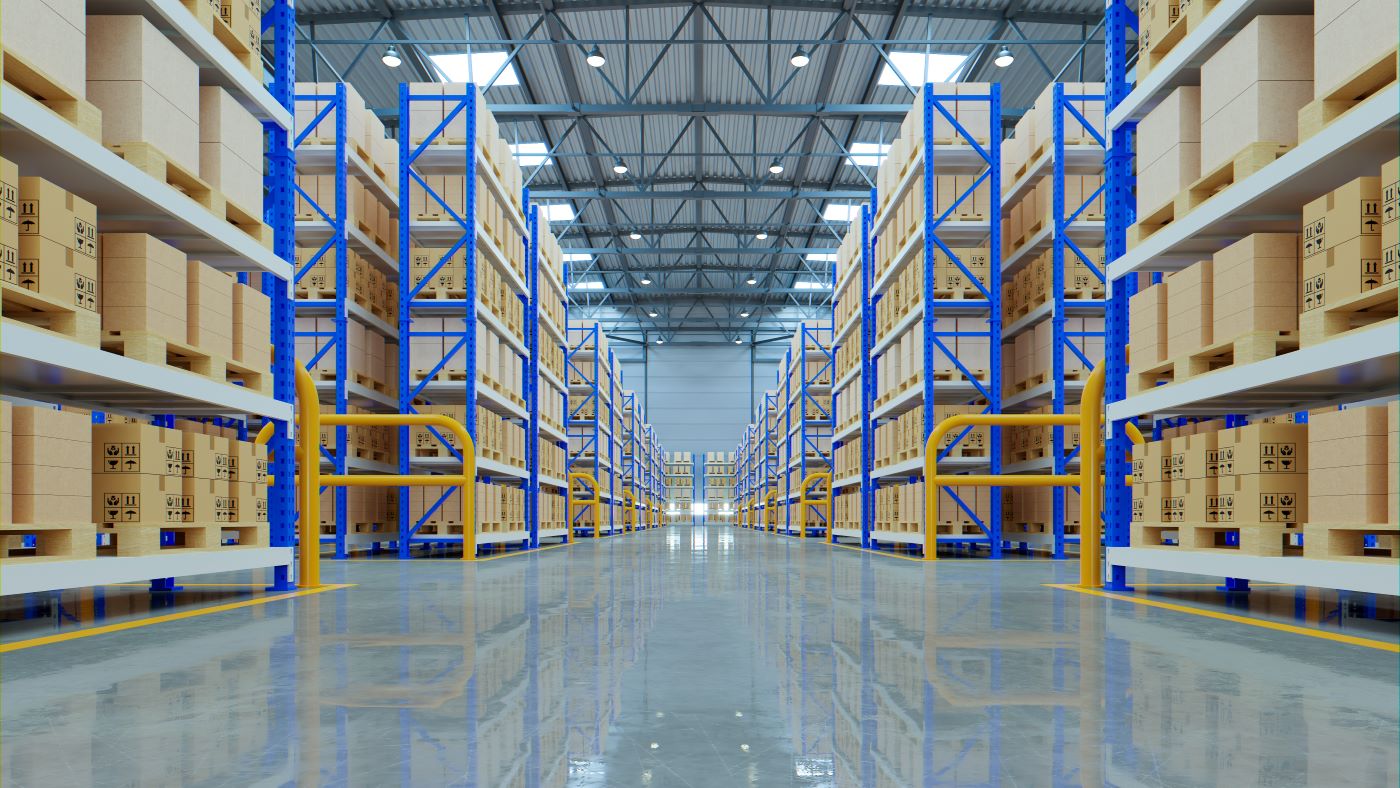
The logistics sector is among the most challenging and complex areas in the business world, encompassing a range of interdependent processes from product receipt and storage to final delivery to customers. To meet customer demands and remain competitive, logistics companies need to be agile, efficient, and innovative. In this context, applying Lean and TPS methodologies can bring significant benefits to companies in this sector, helping reduce waste, improve process efficiency, enhance service quality, provide greater flexibility in customer service, and strengthen customer relationships.
Let’s delve deeper into how Lean and TPS can assist logistics companies in overcoming industry challenges and gaining competitive advantages.
Waste Reduction: Implementing Lean and TPS can help logistics companies reduce waste in time, materials, and resources. For instance, Kanban systems can be used to manage product inventory, preventing over-purchasing and obsolescence losses. Additionally, reducing setup times can decrease equipment idle time and increase process efficiency.
Process Efficiency Improvement: The logistics sector is highly competitive, requiring companies to be agile and efficient to meet customer demands. Lean and TPS applications can help logistics companies improve process efficiency by reducing customer wait times and increasing service capacity. For example, implementing standardized workflows can streamline the order picking and shipping processes, enhancing warehouse productivity.
Service Quality Enhancement: Service quality is a crucial factor in logistics, as it directly impacts customer satisfaction and regulatory compliance. Applying TPS can help logistics companies improve service quality, reducing errors and increasing customer satisfaction. For example, implementing quality monitoring systems can help identify areas for improvement and ensure compliance with safety and quality standards.
Greater Flexibility in Service: The logistics sector is subject to demand fluctuations, which may vary based on seasonality, events, and promotions. By implementing Lean and TPS, logistics companies can become more flexible and responsive to different types of clients, reducing response times and increasing customer satisfaction. For instance, visual management systems can quickly identify high-demand areas, allowing for efficient resource reallocation.
Enhanced Customer Relationships: Customer satisfaction is essential in logistics, as it directly influences customer loyalty and retention. Lean and TPS implementation can help logistics companies strengthen their relationships with customers by increasing transparency and communication. For example, implementing feedback systems can identify areas for improvement and enhance customer satisfaction with the service received.
If you are a professional in this sector seeking ways to improve the efficiency and quality of your processes and services, we highly recommend the implementation of these methodologies.