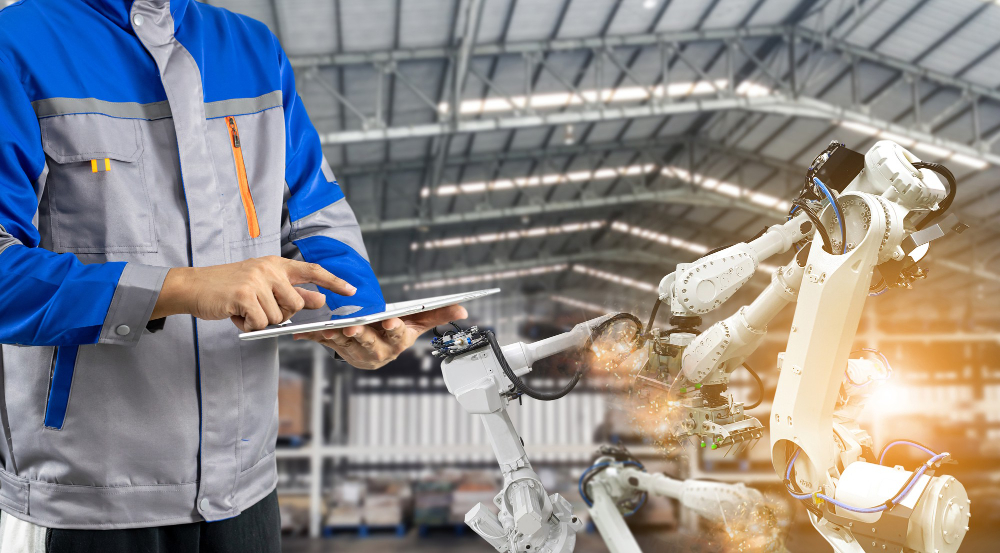
Many people don’t know Mr. Hayashi Nampachi, Toyota’s TPS Sensei.
Hayashi san was one of the last direct disciples of the famous creator of TPS, Taiichi Ohno.
I had the honor of meeting him on one of his visits to Toyota do Brasil in 2011, at the São Bernardo do Campo plant, and of course Mr. Hayashi came to teach us about TPS. At the time, I was working in machining and assembly and had carried out several Kaizens to increase productivity and solve various ergonomic problems.
Recently, watching a lecture by Mr. Hayashi in 2018 on TPS, one of his statements really intrigued me!
The statement was as follows:
“TPS shouldn’t be called TPS (Toyota Production System), it was a mistake!”.
“It should be TPDS (Toyota Process Development System)”.
Mr. Hayashi had stated that the name “TPS – Toyota Production System” was created and approved for use by Mr. Taiichi Ohno himself, and has since been advocated throughout the world.
But why did Mr. Hayashi make this claim, contrary to his mentor Taiichi Ohno?
Why should it be TPDS?
To understand, let’s first talk about the fundamental concepts.
TPS is based on 2 pillars:
Jidouka and Just in Time.
Jidouka is autonomation (Quality in Process):
Stop automatically if any problem occurs => Quality must be built into each process. No defect should be passed on to the next process.
Separate the work of man and machine => Don’t leave man waiting but make maximum use of Manpower.
Error-proof processes.
Just in Time (Right Part, Right Quantity, Right Time):
Takt Time planning.
Continuous Flow.
Pull System.
Quick Changeover.
Logistics integration.
By consistently applying the methodology based on the 2 pillars of TPS, we can achieve our customer satisfaction objectives by guaranteeing high quality products, in the right quantity and at the right time! It is important to remember that the methodology based on these 2 pillars is the basis for consistently reducing costs related to waste in the production process.
But does this alone guarantee that TPS will work?
The answer is “no”.
Before we can erect the pillars, we have to have a solid foundation! This can only be consolidated through visual management, stabilization, process standardization and production levelling.
But in addition to all this, Lean implementation in a company depends on the people who carry out this transformation in their processes.
However, the great insight that Mr. Hayashi shows us here with this change from the much-studied and much-admired TPS to TPDS is directly related to the TOYOTA WAY.
TOYOTA WAY was created in 2001, against a backdrop of high growth for the company and the establishment of several new factories outside Japan. The then president, Fujio Cho, published it and disseminated it to all the plants, in order to curb the weakening of Toyota’s corporate culture during this phase of expansion.
With this publication, Fujio Cho defined Toyota’s DNA, identifying and summarizing unique elements of Toyota’s culture and success.
The Toyota Way is made up of 2 pillars:
Continuous Improvement
Respect for people
Within these 2 pillars are outlined the Management Values and Business Methods that have led Toyota to be so successful and to be the most copied model in companies around the world.
In TOYOTA WAY it becomes clear how Toyota has become a PROCESS DEVELOPER. Every day, faced with increasingly demanding customers and fierce competition, employees are challenged by their superiors to improve their activities and achieve business results.
Valuing people is fundamental to ensuring that processes are increasingly lean (Lead Time and Quality) in a shrewd and consistent manner:
Seeing our customers’ needs.
Looking at the competition, understanding the challenges of the market, and challenging our business.
Training, developing and valuing our employees.
Respecting society.
The Toyota Business Model is a dynamic model in which leaders and employees, faced with market challenges, are developed every day and generate new Kaizen proposals in their processes, which are the starting point for new proposals.
This is why Mr. Hayashi Nampachi came to this conclusion:
The name TPS was a mistake, because the Toyota Model is not just a Production System (TPS), but a Process Development System (TPDS), it is alive and constantly developing, and I would even say that it is missing one more “P”, for People (TPPDS – Toyota Process and People Development System).
In conclusion:
We are coming to the end of the Corona Virus pandemic and our lives have been tremendously changed – wearing masks, working from home, many losing their jobs, confinement, living with family 24 hours a day. I believe that many reflections and changes have arisen in the lives of everyone reading this article. In our companies and our businesses: how have we treated our customers, our employees, our partners, our competitors – and also society – what have we done to leave a legacy?
What do you think about stopping now, before the pandemic ends, for 2, 3 days, a week, to think about your values, and put down on paper what you want to leave for your fellow human beings, be they your children, your friends, your employees, your partners, your neighborhood or city.
Think about it!
Eizo Hanao (e.hanao@honsha.org)
Eizo has worked for Toyota in Brazil and Japan for over 17 years. He specializes in machining, forging and heat treatment. He has implemented lean production lines, Kaizen programs, managed team development plans and process automation.
Click here to read other articles from Honsha.org.
Follow us on YouTube.