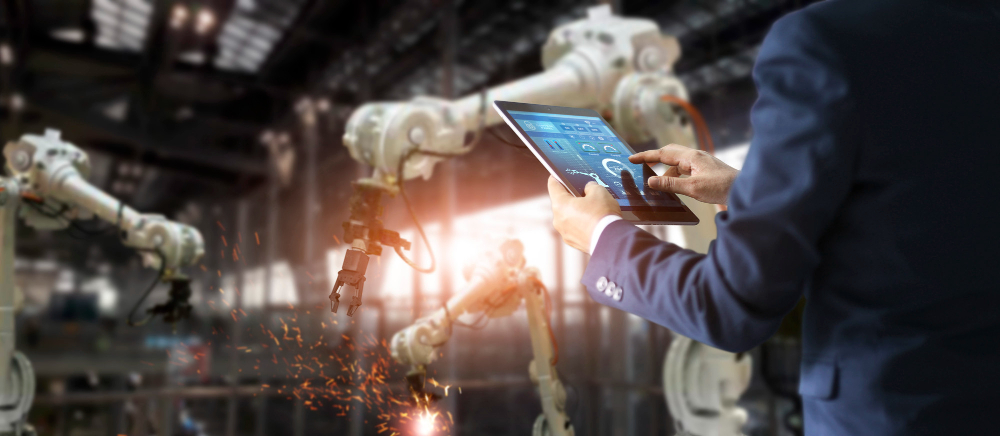
With increasing speed, I see that non-manufacturing organizations are embracing Lean concepts. Some because of the demands of the parent company outside, others because of customer demands, others simply because they realized that there was no other alternative for survival, Lean would be the last attempt to escape the end. This is how, due to the lack of alternatives, the second largest investment bank in the United States began its journey to save millions of dollars. Using standardized work techniques, they changed the sequence of approvals by mortgage brokers. They no longer wasted precious time repeatedly reviewing incomplete applications.
Or like Harvard University, which managed to improve pediatric care at its teaching hospital through techniques such as rapid setup.
There’s also that surf school in San Diego that saw its turnover increase by 85% through Kaizens implemented by the surf instructors themselves. Surfers are friendly enough, but when it comes to Lean, they’re certainly the most reluctant group I’ve worked with. Perhaps they have difficulty with concepts that imply rigidity and discipline.
But once the surfers were convinced of the benefits of the Lean approach, they themselves initiated steps to improve the school, or rather, to save the school from bankruptcy. Here are some of the initiatives:
They implemented visual management, where students were guided by the color of the hangers to find their uniforms more quickly.
They implemented embedded quality, where students self-checked their standing exercises on the boards. They no longer needed an instructor for this long step.
They implemented Poka-Yoke, preventing boards from getting damaged on the transport rack to the beach. They tilted the rack so that there was only one way to pack the boards for transportation.
They implemented student leveling, preventing many younger children from being scheduled in the same class. The risk of such a class is that it increases individual instruction time too much.
They adopted the vision of constantly eliminating waste and increasing added value, to the point where the instructors – who began to notice more idleness due to the Kaizens – were willing to use that time to repair damaged boards (thus increasing capacity) as well as going out to hand out flyers and discount coupons on the beach (thus increasing demand).
It would be very difficult to list the full range of techniques that this school has implemented. But it has shown that there are no limits to where Lean can be applied. Any company that needs to reduce its costs, increase its quality, improve its delivery and services will certainly benefit from this methodology.
Sammy Obara
Sammy learned and implemented the Toyota Production System (TPS) at Toyota facilities in Japan, Brazil, Venezuela and the United States. An expert in Technology Management, he is also a faculty member of the Lean Institute and an instructor of Global Strategy Management at California Community College. He is a guest lecturer for graduate classes at Stanford University and San Diego State University, and has been a speaker at conferences sponsored by the American Production and Inventory Control Society, the Association for Productivity and Quality (APQ), and the American Society for Quality (ASQ). He currently assists companies in implementing Lean through Honsha.org
Click here to read other articles from Honsha.ORG.
Follow us on YouTube.
Your Content Goes Here
Your Content Goes Here
Your Content Goes Here