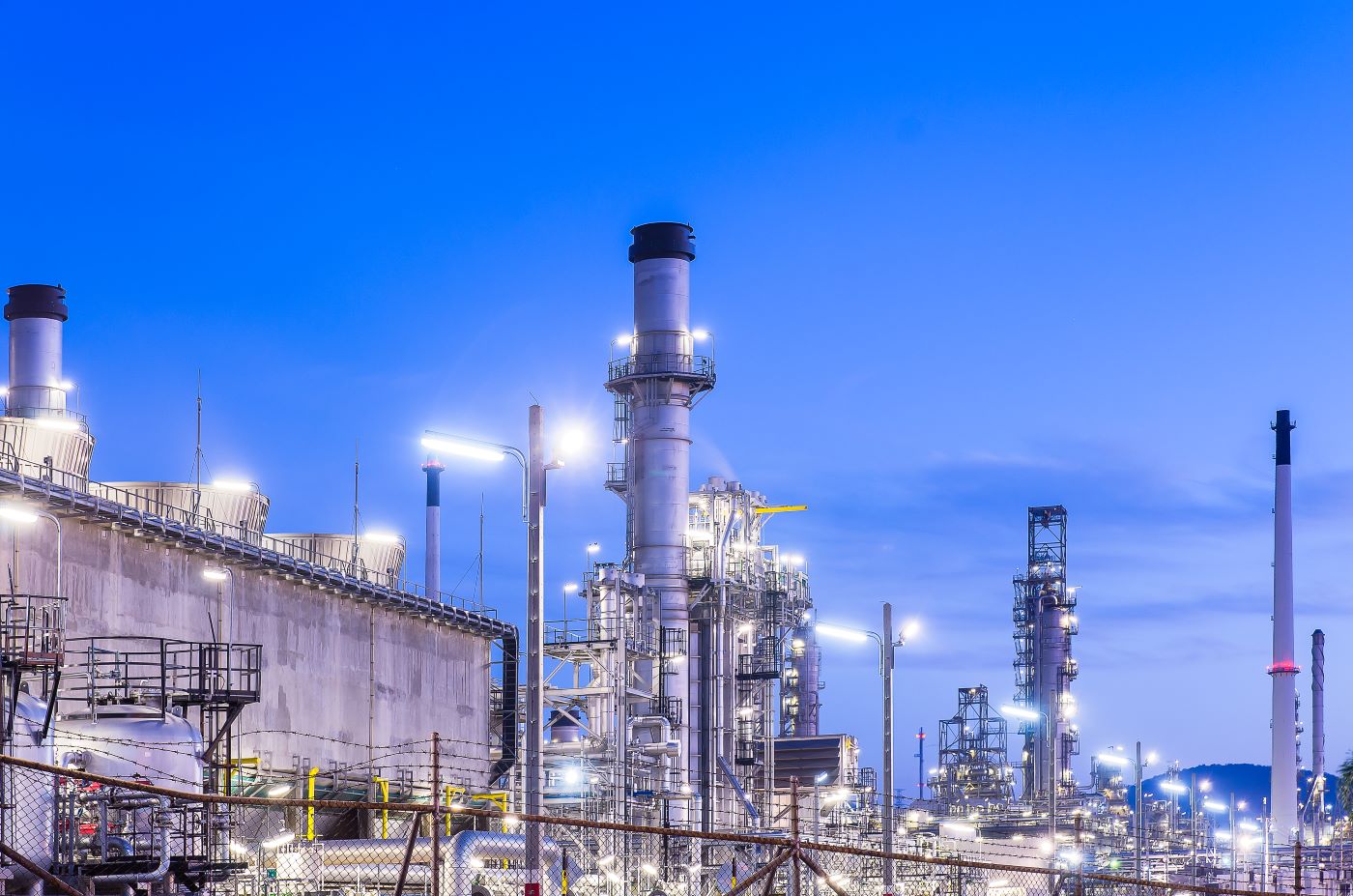
With the growing competitiveness in the fuel market, companies in this sector must find ways to enhance process efficiency, reduce costs, and increase customer satisfaction. An effective approach to achieving these goals is implementing Lean and the Toyota Production System (TPS)—methodologies developed by Toyota and successfully applied across various industries. In this text, we will explore, with practical examples, the exclusive benefits that the fuel sector can achieve by adopting Lean and TPS.
Waste Reduction: The fuel sector deals with products that have a shelf life and may become obsolete over time. Therefore, implementing Lean and TPS can help fuel companies reduce waste in time, materials, and resources. For instance, Kanban systems can help manage fuel inventory, avoiding over-purchasing and loss due to obsolescence. Additionally, reducing setup times can decrease equipment downtime and improve process efficiency.
Enhanced Process Efficiency: The fuel sector is highly competitive, requiring companies to be agile and efficient in meeting customer demands. Lean and TPS can support fuel companies in improving process efficiency, reducing customer wait times, and increasing service capacity. For example, implementing standardized workflows can help decrease vehicle refueling time and increase productivity at fuel stations.
Increased Service Quality: Service quality is crucial in the fuel sector, as it directly impacts customer safety and regulatory compliance. TPS can assist fuel companies in enhancing service quality by minimizing errors and increasing customer satisfaction. For instance, implementing quality monitoring systems can help identify improvement areas and ensure compliance with safety and quality standards.
Greater Flexibility in Service: The fuel sector is subject to demand fluctuations, which can vary based on the time of day, day of the week, and weather conditions. By implementing Lean and TPS, fuel companies can become more flexible and responsive in serving different types of customers, reducing response times and enhancing customer satisfaction. For instance, visual management systems can quickly identify high-demand areas and allow more efficient resource reallocation.
Improved Customer Relations: Customer satisfaction is a key factor in the fuel sector, directly impacting customer loyalty and retention. Implementing Lean and TPS can help fuel companies improve customer relationships by increasing transparency and communication. For example, implementing feedback systems can help identify improvement areas and increase customer satisfaction with service received.
These are just a few examples of how Lean and TPS can bring unique benefits to the fuel sector. If you are a professional in this field and looking for ways to improve the efficiency and quality of your processes and services, we highly recommend adopting these methodologies.