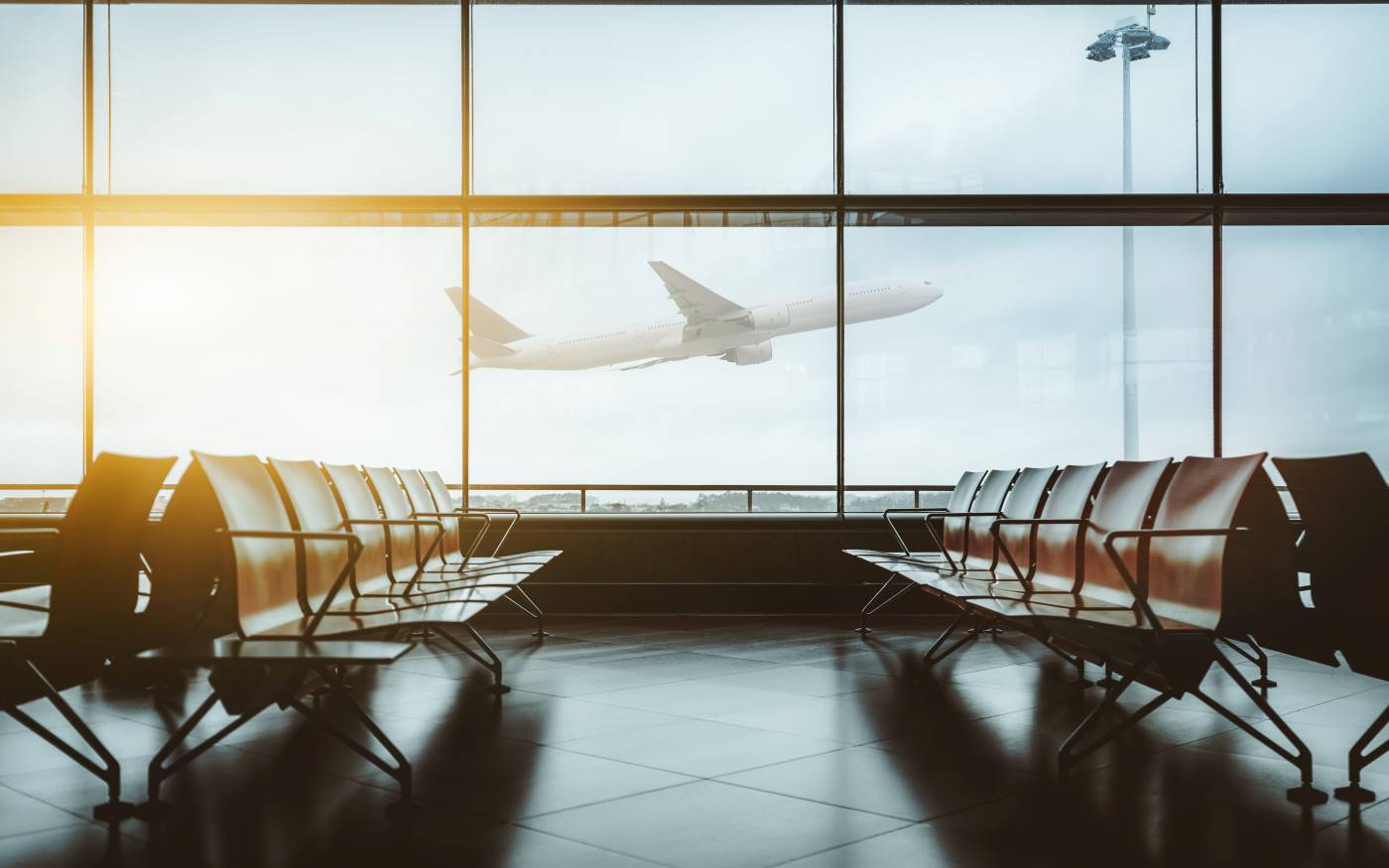
Certainly, the Lean methodology and Toyota Production System (TPS) are not limited to the industrial sector; they can also be applied effectively in the service sector, delivering unique benefits for this area.
The Lean methodology and Toyota Production System (TPS) are widely recognized for their applications in industry, but their potential to enhance service efficiency and quality is often underestimated. In the service sector, these methodologies can bring distinct advantages such as reduced wait times, improved service quality, increased process efficiency, cost reduction, and greater flexibility in service delivery.
Let’s explore these benefits in detail and provide examples of how service companies can apply Lean and TPS to improve their processes and services.
Reduced Wait Times: In service companies, wait time can significantly impact customer satisfaction. Applying Lean and TPS can help reduce wait times by implementing standardized workflows, using Kanban to control workflow, and employing data analysis tools to identify bottlenecks and improvement areas. For example, in a hospital, implementing Lean can help decrease patient wait times for medical care, boosting patient satisfaction.
Improved Service Quality: Service quality is crucial for service companies as it directly affects customer satisfaction and the company’s reputation. Applying TPS can help service companies improve service quality by reducing errors and increasing customer satisfaction. For instance, in a restaurant, implementing TPS can ensure orders are delivered accurately and promptly, enhancing customer satisfaction.
Increased Process Efficiency: In service companies, process efficiency is essential for meeting customer demands and maintaining profitability. Applying Lean can help service companies increase process efficiency, reducing customer wait times and enhancing service capacity. For example, in a bank, Lean implementation can help reduce customer wait times and increase employee productivity.
Cost Reduction: Applying Lean and TPS can help service companies lower costs by eliminating waste and optimizing processes. For example, in an accounting firm, implementing Lean can reduce document processing time, improve employee productivity, and lower operating costs.
Greater Flexibility in Service Delivery: Flexibility in service delivery is crucial for service companies to meet customer demands and remain competitive. By implementing Lean and TPS, service companies can become more agile and responsive to different customer needs, reducing response times and increasing customer satisfaction. For example, in a transportation company, Lean implementation can help reduce customer wait times and offer more flexible travel schedules.