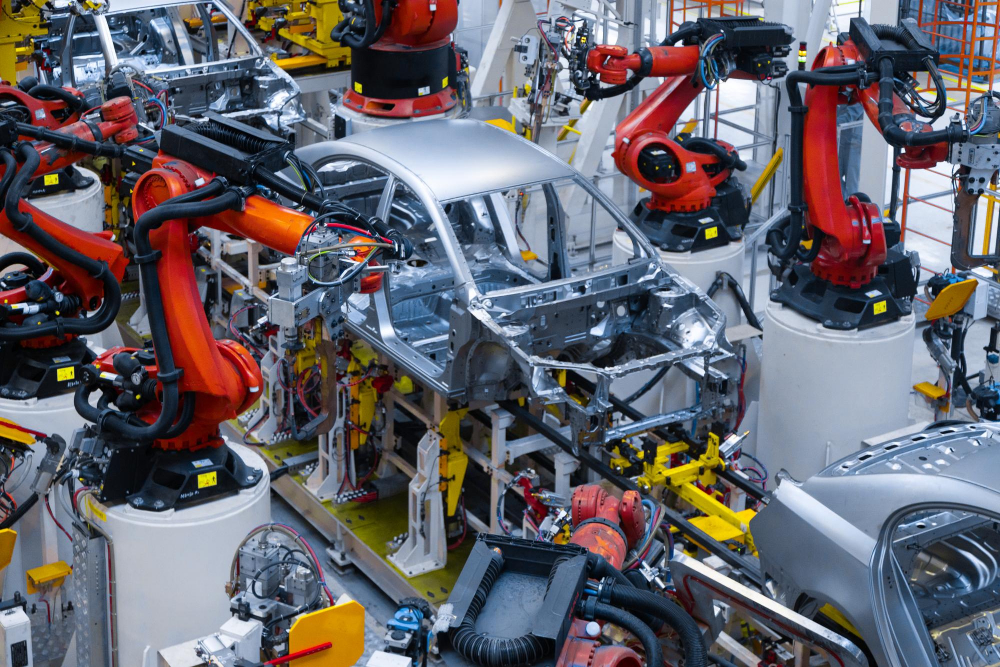
With the growing demand for its vehicles, Toyota expanded its production overseas, i.e. it began building factories in various countries in Asia, Oceania, Europe, Africa and America. These factories were basically built by copying the system, structure, philosophy and concepts that had been practiced at Toyota until then. However, it was observed that the factories outside Japan did not perform as well in terms of productivity and quality when compared to the Toyota factories in Japan.
A thorough investigation was then carried out, followed by a reflection to discover the causes of this difference.
This investigation revealed that
The evaluation criteria differed between the evaluators because there was no standardized way of doing it. Depending on the assessor, the same operator could receive very different assessments. The evaluation criteria and the level to be achieved were vague;
The operating standards were insufficient and incomplete;
Each subsidiary has a “Mother Plant”, i.e. a Toyota plant in Japan that is responsible for the subsidiary. And it was noted that there are differences in procedures and conduct depending on the Mother Plant. This causes a lot of confusion and the subsidiaries don’t know what’s right. In the case of how problems are dealt with, depending on the Parent Plant, the recommended sequence of actions was different from one another.
TMC-Plant A: Restart – Repair – Do not register
TMC-Plant B: Restart – Repair – Record – C/M
TMC-Plant C: Stop – Repair – Restart – Record – C/M – Prevent reoccurrence – Know How
As a result of these differences in performance, the Japanese coordinators (they were employees of the TMC-Toyota Motor Corporation group who worked for an average of three years at the branch) began to ask TMC for training materials for TL and GL. However, TMC didn’t bother to prepare training materials for these levels because the training was mainly done through OJD (On Job Development), i.e. the leader is developed by working for his superior, so there was no training material to meet this request. In TMC’s view, in order for the subsidiaries to maintain good stability and improve their productivity, it was essential to develop human resources. In its assessment, several points of reflection were raised, the main ones being:
Occasional training, unorganized and without personal guidance;
Vague evaluation criteria and expected level;
Focus on technical training and lack of management training;
Lack of standardization between the Parent Plants;
Cultural differences in each subsidiary;
Faced with this problem, TMC’s HR and GPC (Global Production Center) developed a system for developing and managing the shop floor in the 5 missions (Safety, Quality, Productivity, Cost and HR) based on 3 challenges that address “Skill” or Technique, Production Management and Culture, which they called FMDS, which stands for “Floor Management Development System”.
Did you like the subject? Please comment and look forward to future posts.
Eduardo Kiyoshi Yoshihara (e.yoshihara@honsha.org)
Yoshihara has 30 years’ experience working for Toyota in Brazil, Argentina and Japan. A specialist in automotive painting, he also has experience in the areas of plastic injection, resin, the environment and plant maintenance. He was responsible for standardizing FMDS at Toyota Indaiatuba and, together with Toyota TMC senseis, introduced FMDS at Toyota Argentina.
Click here to read other articles from Honsha.ORG.
Follow us on YouTube.
Your Content Goes Here
Your Content Goes Here
Your Content Goes Here