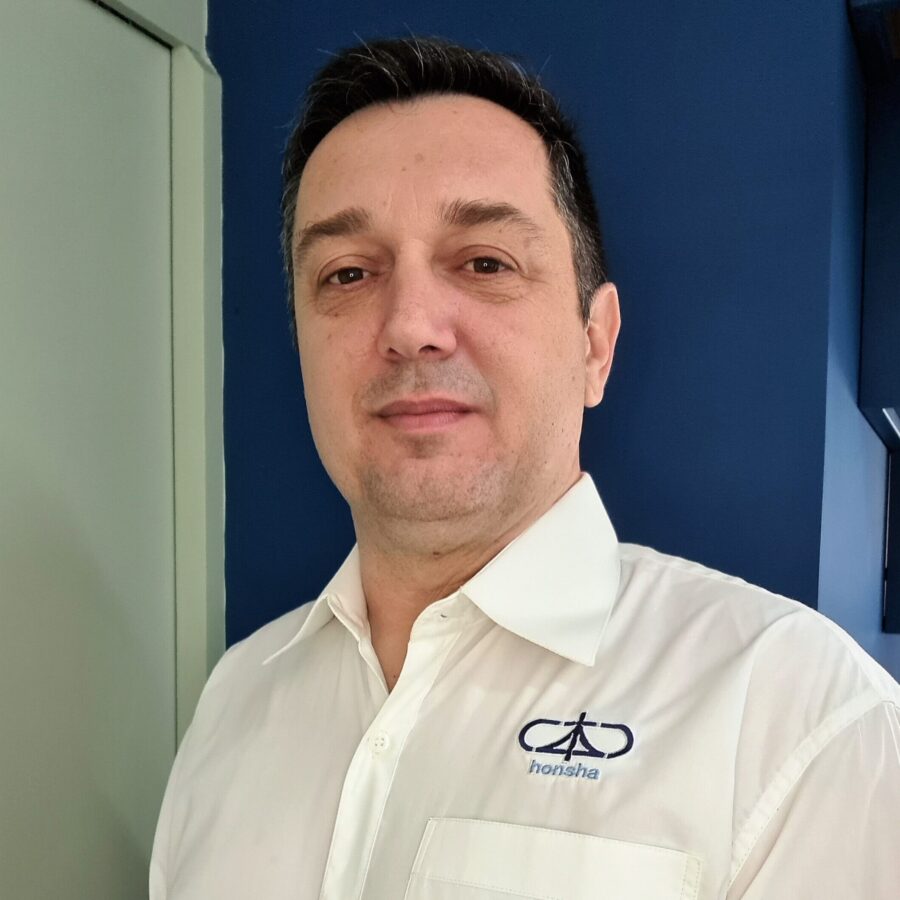
Hello! I’m Alex Grego. I hold a degree in Mechanical Engineering from Santa Cecília University (Santos, Brazil) and in Production and Processes Management (Fatec-Uninter).
Throughout my professional journey, I’ve accumulated twenty-nine years of experience in the automotive and auto parts sector, with seventeen years spent at Toyota do Brasil. During my tenure, I spent five years in the auto parts segment, focusing on manufacturing structural components, bodywork, painting, and external accessories for vehicles such as the VW CrossFox and Fiat Idea. Additionally, I worked for seven years in the fashion and clothing articles segment at Alpargatas, where I oversaw the production of Havaianas sandals as a Manufacturing Process Engineering Manager and as a PMO for various projects, including factory expansions and new technologies.
My journey with Honsha.ORG began in 2012, where I held the position of Senior Associate for three years. I returned to Honsha in 2023, once again assuming the role of Senior Associate.
In terms of projects, I’ve led operational transformations in Brazil and contributed directly to the development of Lean Concepts. Throughout my career, I’ve been involved in significant projects, including operational flow design and the expansion of new business units in the auto parts segment. I played a key role in establishing a dedicated unit for Toyota in Supply Park Sorocaba (Brazil), along with four other new units to serve Volkswagen, GM, and finally Alpargatas. As a PMO for the Masterplan Project and the Digital Journey, I spearheaded initiatives leveraging Power BI and Data Analytics with a focus on Industry 4.0.